Unlike countries such as the US and Australia, the UK has not fully embraced hydro excavation in its civil engineering and infrastructure construction practices.
No doubt deterred by the fears of having to process the resulting bulk of waste mud and clay, this method of excavation in infrastructure development and land remediation remains a pariah for drilling operators. But does it have to be?
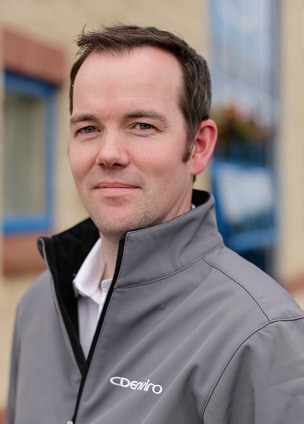
Although trenchless technology has advanced, and hydro excavation has become a more favoured means for installation of services and pipework, it comes with a burden. The by-products of hydro excavation are chemicals and slurry which are difficult to dispose of or reuse responsibly.
Much of the mud is mixed with bentonite, a soft clay which is key to the excavation process because it expands to prevent the collapse of an area during drilling. So even as the engineers benefit from the methodology, the drilling operators are faced with an onerous waste disposal issue at the end.
Recovering treasure using waste treatment
To dispose of the waterlogged, thick mud and clay is financially prohibitive at a landfill site due to its substantial volume and weight. Furthermore, landfill sites are unlikely to accept this bulky waste. Burying it to dry in ponds and fields poses further environmental and legal risk because of its detrimental effect on the land due to possible leaching of hydrocarbons or TPH (total petroleum hydrocarbons). If surrounding land is tested and toxic leaching has damaged the soil then companies are subject to legal action, possibly ruinous for their business.
None of the above disposal methods allow for extraction of any useful materials in the waste mud that can be re-sold, as per the circular economy culture. However, transporting the drilled mud to bespoke waste treatment sites allows for responsible handling of the slurry and recovery of any recyclable materials in it. This method of waste management is legally safer for the drilling company as well as the environment.
However, all is not lost and there are solutions at hand to make hydro excavation a more attractive prospect, without the problematic issues of safe waste by-product disposal.
Process
Processing the waste on site is viable, practical and cost effective. By dealing with it in-situ, it removes the risk of having to transport possibly toxic substances to waste disposal companies and possible leaks or accidents during transport, which is always a danger. However, when transport risks are less, there are viable solutions for ex-situ processing too.
Modern technology allows for safe dewatering of clay onsite and off-site, with an added ability to extract any useful materials from it for re-use. These re-usable materials may include sand, stone and organics with recyclable value as new revenue streams.
Effective solutions such as ours include bespoke reception centres for hydro excavation waste, where valuable materials are recoverable for re-sale. Furthermore, the recovered water can be treated for re-use.
Benefits
There are workable solutions to the hydro excavation waste burden.
Fergal Campbell
CDEnviro
The benefits of this approach afford customers greater control of their waste, a more sustainable approach to processing it, reduced disposal costs and added value with recoverable materials.
There are workable solutions to the hydro excavation waste burden, making it easier for contractors to use a tried and tested method of excavation without the unpleasant conundrum of how to clean up responsibly afterwards.
It also reduces the legal, as well as environmental risks. With this type of waste processing solution at hand, hydro-excavation doesn’t have to be the poisoned chalice; instead it can be the sustainable gift that keeps on giving.
Subscribe for free